Industrial Markets
Reducing costs and emissions with waste heat recovery
The industrial markets provide the setting for innovative thermoelectric power generation in the mid to long-term and consequently, the far-reaching, scalable deployment of MicroPower’s technology.
The most exciting area of application for MicroPower's technology is industrial waste heat recovery which thermoelectrics has been promising to tackle for many years, but has not been achievable thus far due to low efficiencies, low temperatures and high cost.
Big industry is by far the largest consumer of energy globally, with energy-intensive processes requiring vast amounts of electricity and accounting for 42% of global consumption (9362 TWh) in 2018 according to the IEA, compared to 2% for transportation, 27% for residential, and 22% for commercial.
Of course, without even considering the processes themselves, this means that industry is responsible for a significant portion of carbon emissions as power production is still dominated by fossil fuels despite the encouraging trend towards greener forms of electricity generation.
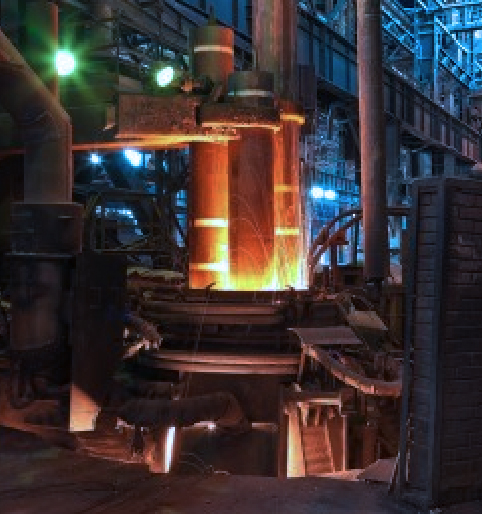
Process Waste Heat Recovery
Steel and glass furnaces, aluminium and magnesium smelters, cement production, and oil & gas refining are all examples of industrial processes which require vast amounts of electricity yet also produce large quantities of waste heat. Some of this can be recycled by conventional means, but not all – either because the temperature is too low, or because one can’t physically reach the heat using existing technologies.
For minimal additional operating cost, a portion of this essentially free energy can be recovered and converted into electricity by using waste heat recovery systems based on MicroPower’s technology. The double benefit is a reduction of heat load and the production of electricity without significantly increasing costs.
Remote Power Sources
Remote oil pipeline monitoring, off-shore engineering, insect-eradication and remote telemetry and data collection are examples of situations that require power, but where conventional grid electricity is not available, solar panels aren’t feasible, the use of batteries is impractical or impossible, and reliability is key.
Power generation systems using thermoelectric modules have long been used for such applications, burning natural gas or propane as a heat source, or using a decaying nuclear isotope when the location is very isolated, such as space, or remote unmanned lighthouses. Of course, with the higher temperature profile and greater efficiency of MicroPower’s devices, more power is generated from the same amount of fuel.
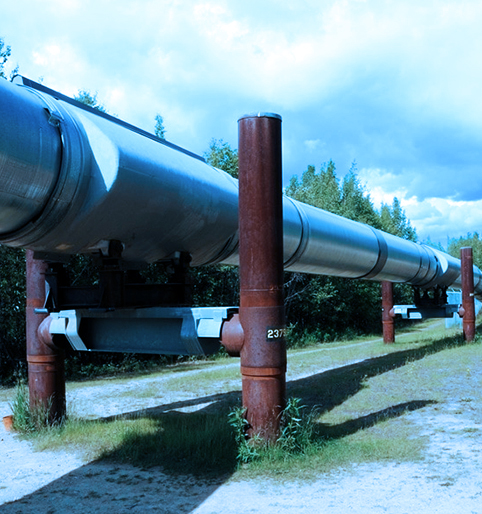
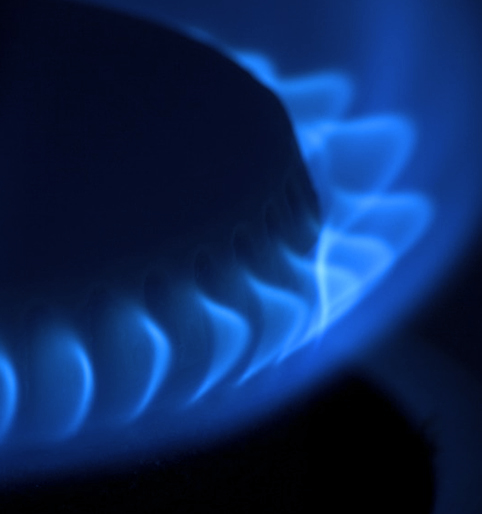
Pilot Flame Applications
Many gas-fed heating appliances use a basic thermocouple, placed in the pilot flame, to generate a voltage which operates the supply valve which feeds gas to the pilot. So long as the pilot flame remains lit, the thermocouple remains hot, and the pilot gas valve is held open. If the light goes out, the thermocouple temperature falls, causing the voltage to drop and the valve to close.
Today’s more energy-conscious manufacturers are aware that having a constantly burning flame does not aid energy efficiency and so are interested in replacing the thermocouple with an advanced thermoelectric device that can produce much more electricity, opening up the possibility of using pilot heat not simply as a fail-safe mechanism, but also to power the electronic displays.
Gas Flare Stacks
Associated hydrocarbon gas from oil fields all over the world is being flared in large volumes. There is a worldwide effort to reduce the amount of gas flaring but the reality is that huge volumes will continue to be flared for many years to come. A very few of these “candle” flares have heat recovery units attached to convert the heat to useful electrical or thermal energy.
The incremental cost to make electric power from these flares is very high, especially since flaring is intermittent and unreliable and a Rankine cycle will easily be upset with the start/stops and transients associated with the flare. Replacing these types of heat recovery units with MicroPower devices would aid the efficiency of electric power production, with significantly lower costs.
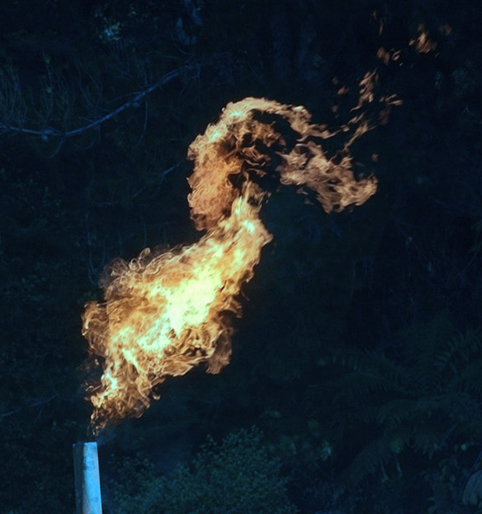
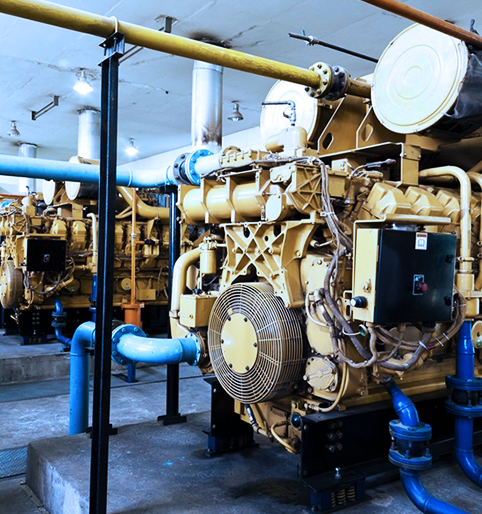
Reciprocating Generator Engines
Diesel and gas reciprocator engines are generally used to provide electrical power in areas where utility electricity is unavailable, or only needed temporarily, and there are a variety of commercial, industrial and municipal applications – particularly renewable and waste-to-energy industrial power generation, cogeneration/CHP, and oilfield power generation.
Reciprocating engine generators often do have some hot water or other form of waste heat recovery feature available, but adding an Organic Rankine Cycle for additional power is rarely done. The problem is often a combination of the space required, significant capex, and high operating and maintenance requirements and costs, making MicroPower’s technology a desirable alternative.